“We run a mixed shop‑floor: legacy machines without digital interfaces alongside newer, smart‑enabled equipment. What should be our AI-ready strategy?”
This is one of the most frequently asked questions we’ve encountered from more than 100 production managers, CEOs, and innovation leads across the manufacturing sector. It’s a real, tangible challenge for factories everywhere: how do you build a consistent digital strategy when your machines speak different languages—or none at all?
With Industry 4.0 now becoming the baseline rather than the aspiration, the need for integrating both old and new machinery into a unified, AI-ready infrastructure is no longer optional. It’s foundational for staying competitive, responsive, and efficient.
This blog post explores how manufacturing companies can move from this fragmented baseline toward a seamless AI-ready environment—without replacing their existing machines. We’ll start with a general overview of the strategy behind retrofitting and standardization, then dive into a deeper technical discussion, and finally close with practical recommendations you can act on today.
Why Retrofitting is the Foundation of AI in Manufacturing
In a perfect world, every machine on the shop floor would be AI-ready out of the box. But the reality is very different—especially in small and mid-sized enterprises (SMEs). Most production lines today are “mixed environments”: some machines were installed decades ago, while others are brand-new and come with built-in smart capabilities. The challenge lies in unifying these systems into one coherent data architecture.
This is where retrofitting becomes crucial. Retrofitting refers to equipping older, non-digital machines with external sensors and interfaces that allow them to communicate operational data. Instead of replacing perfectly functional equipment—an extremely costly and disruptive process—companies can bridge the digital gap and bring legacy assets into the AI era.
The logic is simple but powerful:
-
You don’t need every machine to be smart.
-
You need every machine to be visible.
Once visibility is established—through vibration sensors, power meters, microphones, or temperature probes—you can begin to standardize the data. The next step is to stream that data through middleware platforms (either on the edge or in the cloud) that structure and normalize it for further use.
When combined with the structured data from newer smart-enabled machines, you now have a unified data layer. This layer becomes the backbone of advanced applications: dashboards, alerts, predictive analytics, and eventually—AI-driven decision-making.
Far from being a compromise, retrofitting is now a proven strategy adopted across leading manufacturing sectors. It’s fast to implement, cost-effective, and flexible enough to scale with the business.
Next, we’ll dive deeper into how this strategy works in practice: what components are needed, what kinds of data are most useful, and how it all flows together into an AI-ready system.
Building an AI-Ready Architecture — Step by Step
Creating an AI-ready shop-floor when you operate a mix of legacy and modern machines requires a layered, modular approach. At Novo AI, we’ve developed a four-step methodology that has been successfully deployed in dozens of industrial settings. Here’s how it works in detail:
1. Sensor-Based Retrofitting: Making Legacy Machines Speak
Most older machines don’t expose digital outputs—but they still emit signals. The first step is to capture these signals:
Vibration Sensors: Reveal machine behavior such as idling, operation, or failure patterns.
Acoustic Sensors: Capture process-specific sound signatures, such as cutting, pressing, or stopping.
Temperature Sensors: Indicate abnormal heat buildup, useful in both mechanical and electrical systems.
Current Transformers (CTs): Monitor energy usage and indirectly reveal machine states.
Sensors are mounted non-invasively—no need to access the machine’s control logic or PLC. This avoids the risk of invalidating warranties or damaging systems. All data is timestamped at the source and pushed to an edge device for initial processing.
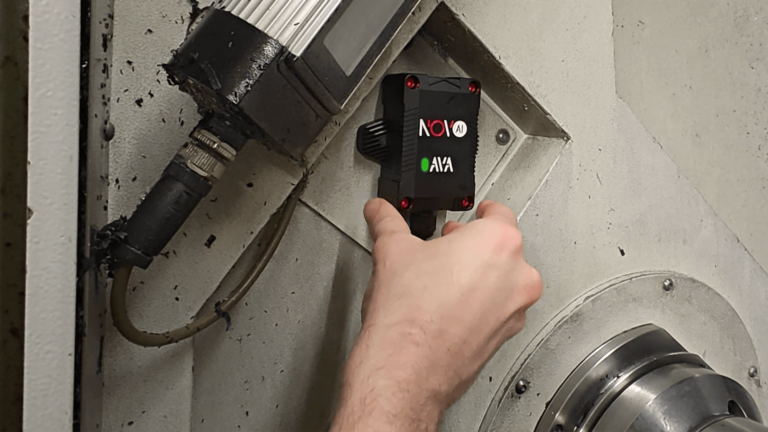
2. Edge-Based Middleware: Translating Signals into Structured Data
Once raw sensor data is collected, the next step is normalization:
-
Our edge device uses embedded AI models and rule-based logic to classify machine states in real time: Production, Idle, Off, or Error.
-
These classifications are computed locally using signal processing and machine learning techniques, minimizing latency.
-
All outputs are converted into a common schema (e.g., JSON or MQTT topics), regardless of the original machine or sensor type.
This ensures a plug-and-play interface with your broader IT or cloud systems.
3. Data Integration: Creating Operational Transparency
The structured machine data is sent to a central platform (cloud or on-premise), where it can be:
Visualized in real-time dashboards
Mapped against shift schedules, operator inputs, or production targets
Analyzed historically for trends, downtime causes, and OEE (Overall Equipment Effectiveness) improvement
This provides plant managers and operations teams with end-to-end transparency—a unified view across legacy and modern assets.
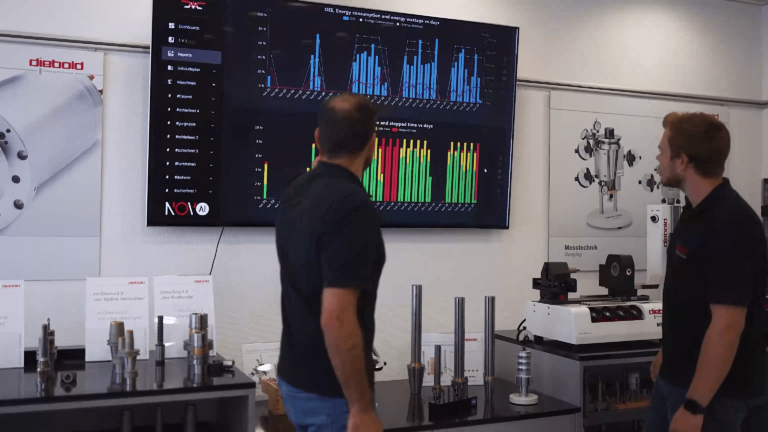
4. AI-Driven Optimization: Closing the Feedback Loop
The final—and most powerful—layer is AI integration:
Trained machine learning models detect patterns in machine usage, idle times, tool wear, or production bottlenecks.
These insights can trigger automated actions: maintenance requests, shift reassignments, or even production rerouting.
Operators receive explainable, prioritized suggestions instead of raw alarms.
Critically, Novo AI doesn’t just display data—it understands it and helps you act on it.
No rip-and-replace. No IT chaos. Just scalable intelligence, built on the machines you already have.
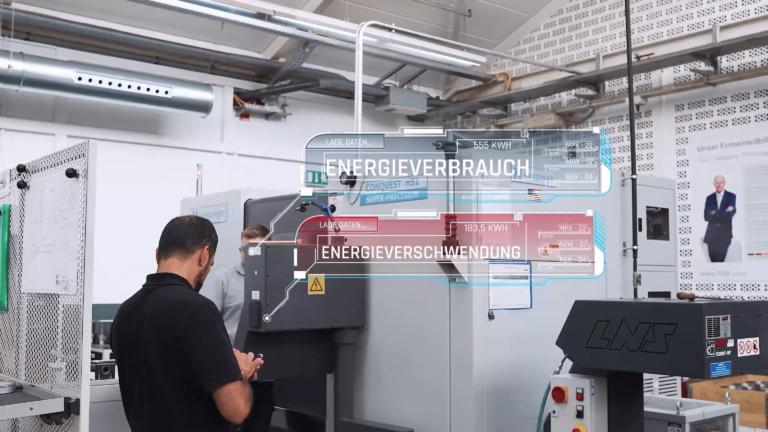
The question we started with “What should be our AI-ready strategy for a mixed shop-floor?”—is not a future problem. It’s a now problem. But it’s also a solvable one.
🚀 You don’t need to replace your legacy machines.
🚀 You don’t need to wait until everything is “smart.”
With the right retrofit sensors, edge intelligence, and AI-ready infrastructure, your entire shop-floor—new or old—can become fully transparent, measurable, and optimizable. This approach isn’t just about data; it’s about creating a connected, responsive factory that learns, adapts, and continuously improves.
At Novo AI, we’ve helped manufacturers of all sizes—from specialized job shops to high-volume producers—turn fragmented machine environments into harmonized, AI-powered systems. And we can help you do the same.
🚀 Ready to unlock the full potential of your machines?