„Wir betreiben eine gemischte Produktionsumgebung – mit älteren Maschinen ohne digitale Schnittstellen und modernen, smarten Anlagen. Was ist unsere Strategie, um AI-ready zu werden?“
Diese Frage haben uns über 100 Produktionsleiter, Geschäftsführer und Innovationsverantwortliche aus der Fertigungsindustrie gestellt. Und sie ist absolut berechtigt: Wie entwickelt man eine digitale Strategie, wenn die Maschinen auf dem Shopfloor unterschiedliche – oder gar keine – Sprachen sprechen?
Da Industrie 4.0 inzwischen nicht mehr Vision, sondern Standard ist, ist die Integration von Alt- und Neumaschinen in eine gemeinsame, KI-fähige Infrastruktur längst kein Nice-to-have mehr. Sie ist zur Grundlage geworden, um wettbewerbsfähig, anpassungsfähig und effizient zu bleiben.
In diesem Blogbeitrag zeigen wir, wie produzierende Unternehmen diesen fragmentierten Ausgangspunkt in eine durchgängige, AI-bereite Umgebung überführen können – ohne bestehende Maschinen auszutauschen. Wir starten mit einem Überblick über die Retrofitting-Strategie, steigen dann tiefer in die technische Umsetzung ein und schließen mit konkreten Handlungsempfehlungen ab.
Warum Retrofitting die Grundlage für KI in der Fertigung ist
In einer idealen Welt wären alle Maschinen auf dem Shopfloor von Anfang an KI-fähig. Die Realität sieht jedoch anders aus – vor allem im Mittelstand. Viele Produktionslinien bestehen aus einem Mix: Maschinen, die seit Jahrzehnten im Einsatz sind, stehen neben neu angeschafften, smarten Anlagen. Die große Herausforderung besteht darin, diese heterogene Landschaft in eine einheitliche Datenarchitektur zu überführen.
Hier kommt das Thema Retrofitting ins Spiel. Dabei werden ältere Maschinen mit externen Sensoren und Schnittstellen nachgerüstet, sodass sie betriebliche Daten erfassen und übermitteln können. Anstatt funktionierende Maschinen zu ersetzen – ein kostenintensiver und oft unnötiger Schritt – wird so die digitale Kluft effizient überbrückt.
Die Logik dahinter ist einfach, aber wirkungsvoll:
-
Nicht jede Maschine muss smart sein.
-
Aber jede Maschine muss sichtbar sein.
Sobald diese Sichtbarkeit über Vibrations-, Strom-, Geräusch- oder Temperatursensoren hergestellt ist, lässt sich die gewonnene Information standardisieren. Die erfassten Signale werden anschließend über Middleware – entweder lokal am Edge oder in der Cloud – in ein einheitliches, KI-lesbares Format übersetzt.
Gemeinsam mit strukturierten Daten aus modernen Maschinen entsteht so eine einheitliche Datengrundlage. Diese bildet das Rückgrat für Dashboards, Benachrichtigungen, Predictive Analytics und letztlich für KI-gestützte Entscheidungen.
Im nächsten Abschnitt zeigen wir Schritt für Schritt, wie sich diese Strategie konkret umsetzen lässt.
So entsteht eine AI-Ready Architektur
Wenn Alt- und Neumaschinen nebeneinander arbeiten, braucht es eine klare, modulare Architektur, um AI-Readiness zu erreichen. Bei Novo AI haben wir dafür ein vierstufiges Vorgehen entwickelt, das sich in zahlreichen Projekten bewährt hat:
1. Retrofitting mit Sensoren – Alte Maschinen zum Sprechen bringen
Auch wenn ältere Maschinen keine digitalen Ausgänge besitzen, senden sie trotzdem Signale:
Vibrationssensoren: zeigen Zustände wie Produktion, Leerlauf oder Störungen an.
Akustiksensoren: erfassen prozessspezifische Geräusche wie Schneiden, Pressen oder Anhalten.
Temperatursensoren: identifizieren ungewöhnliche Hitzeentwicklung – mechanisch wie elektrisch.
Stromsensoren (CTs): überwachen Energieverbrauch und ermöglichen Rückschlüsse auf den Maschinenzustand.
Diese Sensoren werden berührungslos montiert – ein Eingriff in die Maschinensteuerung ist nicht nötig. Damit bleiben Garantien erhalten, Risiken werden vermieden. Die Daten werden direkt am Sensor mit Zeitstempel erfasst und an ein Edge-Gerät übertragen.
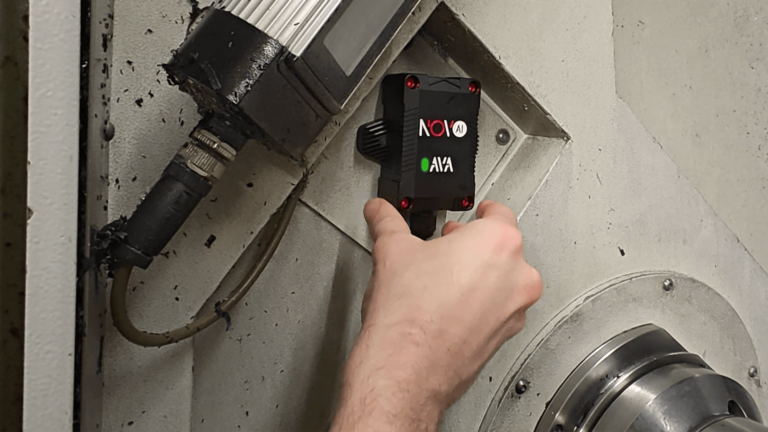
2. Edge-Middleware – Signale in strukturierte Daten übersetzen
Nach der Datenerfassung folgt die Normalisierung:
-
Unsere Edge-Geräte nutzen KI-Modelle und regelbasierte Logik, um Maschinenzustände in Echtzeit zu klassifizieren: Produktion, Leerlauf, Aus, Störung.
-
Die Analyse erfolgt lokal – so bleiben Latenzen minimal.
-
Alle Daten werden in ein standardisiertes Format gebracht (z. B. JSON oder MQTT) – unabhängig von Maschinentyp oder Sensortechnik.
So entsteht eine Plug-and-Play-Schnittstelle zu bestehenden IT- oder Cloud-Systemen.
3. Datenintegration – Operative Transparenz schaffen
Die strukturierten Maschinendaten werden an eine zentrale Plattform (Cloud oder lokal) übertragen und können dort:
In Echtzeit visualisiert werden
Mit Schichtplänen, Zielvorgaben oder Bedienereingaben verknüpft werden
Historisch analysiert werden (Stillstandsgründe, OEE, Trends)
Das Ergebnis: volle Transparenz, über alle Maschinen hinweg – alt wie neu.
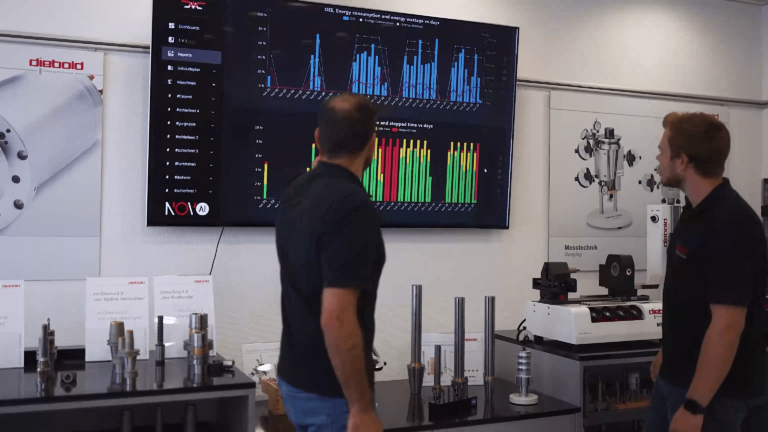
4. KI-gestützte Optimierung – Den Kreis schließen
Im letzten Schritt werden die Daten durch KI-Modelle genutzt:
Algorithmen erkennen Muster bei Maschinenlaufzeiten, Leerlauf, Werkzeugverschleiß oder Engpässen.
Daraus entstehen konkrete Handlungsempfehlungen: Wartungsbedarf, Umplanung, Alarmpriorisierung.
Bediener erhalten keine rohen Alarme, sondern erklärbare, priorisierte Hinweise.
Der entscheidende Punkt: Novo AI zeigt nicht nur Daten – wir verstehen sie und leiten daraus klare Handlungen ab.
Kein Austausch. Kein IT-Chaos. Nur skalierbare Intelligenz – aufgebaut auf dem Maschinenpark, den Sie bereits haben.
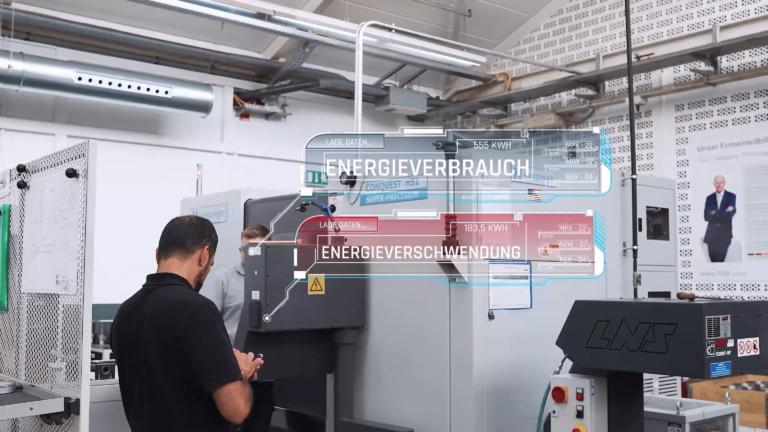
Die eingangs gestellte Frage – „Was ist unsere AI-Ready-Strategie bei gemischtem Maschinenpark?“ – betrifft nicht die Zukunft. Sie betrifft das Hier und Jetzt. Und sie ist lösbar.
🚀Sie müssen keine Altmaschinen ersetzen.
🚀 You don’t need to wait until everything is “smart.”
Mit den richtigen Retrofit-Sensoren, intelligenter Middleware und einem AI-fähigen Datenfundament wird aus Ihrer Produktion ein vernetztes, lernendes System – ganz unabhängig vom Maschinenalter.
Novo AI hat bereits zahlreiche Unternehmen dabei begleitet, aus fragmentierten Shopfloors harmonisierte, KI-gestützte Produktionslandschaften zu machen. Und wir können auch Sie dabei unterstützen.
🚀 Bereit, das volle Potenzial Ihrer Maschinen zu entfesseln?