Wie verbinde ich ältere Maschinen meines Maschinenparks in das ERP? Wichtige Schritte zur Maschinenüberwachung für eine effiziente Integration
Die Integration älterer Maschinen in ein modernes ERP-System stellt viele Produktionsunternehmen vor eine große Herausforderung. Während moderne Maschinen oft bereits mit digitalen Schnittstellen ausgestattet sind, fehlen bei älteren Anlagen oft die nötigen Voraussetzungen für eine nahtlose Integration. Dies führt zu einem fragmentierten Maschinenpark, in dem einige Prozesse digital überwacht werden können, während andere auf manuelle Datenerfassung angewiesen sind.
Gerade in der heutigen Zeit, in der Effizienz, Transparenz und Automatisierung entscheidende Wettbewerbsvorteile darstellen, ist es für Unternehmen unerlässlich, eine Lösung für dieses Problem zu finden. Eine effektive Maschinenüberwachung und Maschinendatenerfassung kann hier die Brücke zwischen alten Maschinen und modernen ERP-Systemen schlagen. Doch welche Herausforderungen gibt es bei der Integration und welche Technologien – wie Echtzeitüberwachung oder digitale Dashboards – helfen bei der Umsetzung? In diesem Artikel erfahren Sie, wie Sie ältere Maschinen effizient in Ihr ERP-System einbinden und so Ihre Produktionsprozesse optimieren können.
Warum ist die Integration älterer Maschinen in das ERP-System wichtig?
Die Digitalisierung in der Industrie schreitet mit großen Schritten voran. Unternehmen, die weiterhin auf analoge Prozesse setzen, geraten ins Hintertreffen. Ohne eine zuverlässige Maschinendatenerfassung fehlt es an wichtigen Kennzahlen zur Produktionsleistung, Wartung und Energieeffizienz. Dies führt zu ineffizienten Prozessen, fehlender Transparenz und steigenden Kosten.
Eine erfolgreiche ERP-Integration älterer Maschinen bietet zahlreiche Vorteile:
- Echtzeitdaten statt Schätzungen: Die Echtzeitüberwachung ermöglicht es, jederzeit aktuelle Informationen über Maschinenlaufzeiten, Stillstände und Produktionsauslastung abzurufen.
- Bessere Entscheidungsgrundlage: Durch eine präzise Maschinendatenerfassung werden datenbasierte Entscheidungen möglich, die Effizienz und Produktivität steigern.
- Weniger manuelle Arbeitsschritte: Ohne digitale Anbindung müssen Maschinenbediener oft Daten manuell erfassen und in das ERP-System übertragen – ein Prozess, der fehleranfällig und zeitaufwendig ist.
- Geringere Wartungskosten: Unternehmen, die Maschinenlaufzeiten und -zustände kontinuierlich überwachen, können Wartungen gezielt planen und teure Ausfälle vermeiden.
- Erhöhte Wettbewerbsfähigkeit: Wer seinen Maschinenpark digitalisiert, kann flexibler auf Marktveränderungen reagieren, Kosten senken und seine Produktionskapazitäten besser nutzen.
Ohne eine nahtlose Integration kann es passieren, dass Unternehmen wertvolle Produktionsdaten nicht nutzen und ineffiziente Prozesse weiterhin bestehen bleiben. Doch warum ist es so schwierig, ältere Maschinen an moderne Systeme anzubinden?
Herausforderungen bei der ERP-Integration älterer Maschinen
Viele Unternehmen stehen bei der Integration vor ähnlichen Problemen: Ihre Maschinen sind in einem guten Zustand, aber die fehlende digitale Anbindung erschwert eine effiziente Nutzung. Besonders folgende Herausforderungen treten häufig auf:
- Fehlende Schnittstellen: Ältere Maschinen haben oft keine standardisierten Kommunikationsprotokolle wie OPC UA oder MQTT. Stattdessen arbeiten sie mit proprietären Steuerungen oder gar ohne digitale Datenübertragung.
- Uneinheitliche Datenformate: Maschinen unterschiedlicher Hersteller liefern Daten in verschiedenen Formaten, die nicht direkt mit einem ERP-System kompatibel sind. Eine Optimierung dieser Datenströme erfordert spezielle Software oder Middleware.
- Manuelle Datenerfassung: In vielen Betrieben erfolgt die Erfassung von Maschinenlaufzeiten, Stillständen oder Produktionsmengen noch händisch – ein zeitintensiver und fehleranfälliger Prozess.
- Hoher Anpassungsaufwand: Selbst wenn Maschinen bereits über eine digitale Schnittstelle verfügen, müssen oft individuelle Anpassungen vorgenommen werden, damit die Daten mit dem ERP-System kompatibel sind.
- Hohe Nachrüstungskosten: Manche Unternehmen scheuen sich vor der Investition in neue Hard- und Softwarelösungen, da sie hohe Kosten fürchten. Dabei gibt es heute kosteneffiziente Retrofit-Lösungen, die eine Integration erleichtern.
Diese Herausforderungen zeigen, dass eine durchdachte Strategie notwendig ist, um ältere Maschinen erfolgreich in ein modernes ERP-System einzubinden. Unternehmen sollten daher nicht nur auf eine reine Maschinendatenerfassung setzen, sondern auch auf intelligente Maschinenüberwachung und benutzerfreundliche Dashboards, die eine einfache Analyse und Visualisierung der Daten ermöglichen.
Maschinenüberwachung: Ein Schlüssel zur erfolgreichen Integration
Schritte zur Integration älterer Maschinen
Die Integration älterer Maschinen in Ihr ERP-System erfordert einen strukturierten Ansatz. Hier sind die wesentlichen Schritte, die beachtet werden sollten:
1. Bestandsaufnahme der Maschinen
Der erste Schritt jeder erfolgreichen Integration ist eine detaillierte Bestandsaufnahme. Unternehmen sollten klären, welche Maschinen über digitale Schnittstellen verfügen und wo es noch Lücken gibt.
Folgende Fragen sollten in dieser Phase beantwortet werden:
- Welche Maschinen sind bereits digital vernetzbar, welche benötigen eine Nachrüstung?
- Welche Datenformate und Protokolle werden von den Maschinen unterstützt? (z. B. OPC UA, Modbus, MQTT)
- Gibt es bereits eine vorhandene Maschinendatenerfassung, die in das ERP-System integriert werden kann?
- Wie werden Maschinenlaufzeiten, Stillstände und Produktionskennzahlen aktuell erfasst?
- Gibt es eine zentrale Dashboard-Lösung, die Maschinen- und Produktionsdaten übersichtlich visualisiert?
Nach dieser Bestandsaufnahme wird klar, welche Maschinen direkt angebunden werden können und wo Retrofit-Technologien erforderlich sind.
2. Auswahl der Integrationslösung
Sobald die Bestandsaufnahme abgeschlossen ist, geht es darum, die passende Lösung für die Anbindung der Maschinen an das ERP-System zu wählen. Hier gibt es mehrere Ansätze:
1. Middleware-Software als Schnittstelle nutzen
Falls ältere Maschinen keine moderne Schnittstelle besitzen, kann eine Middleware helfen. Diese Software fungiert als Vermittler zwischen Maschine und ERP-System, indem sie Daten in ein kompatibles Format umwandelt.
Vorteile:
✅ Ermöglicht die Maschinendatenerfassung auch für ältere Anlagen
✅ Reduziert den Aufwand für individuelle Anpassungen
✅ Funktioniert mit vielen bestehenden Maschinensteuerungen
2. Retrofit-Lösungen mit IoT-Sensoren einsetzen
Falls Maschinen gar keine digitalen Schnittstellen haben, können externe IoT-Sensoren installiert werden. Diese Sensoren erfassen beispielsweise (Hier gibt es mehr Informationen zu Retrofit-Lösungen):
- Vibrationen und Schwingungen (Zustände automatisiert erkennen)
- Energieverbrauch (zur Optimierung der Betriebskosten)
- Betriebszustand (Laufzeit, Stillstände, Produktionsmengen)
Diese Daten können anschließend in ein Dashboard eingespeist werden, das eine Echtzeitüberwachung der Maschinen ermöglicht.
Vorteile:
✅ Funktioniert unabhängig von Maschinentyp und Hersteller
✅ Keine tiefgreifenden Änderungen an der Maschinensteuerung nötig
✅ Kostengünstige Alternative zur vollständigen Maschinenmodernisierung
3. Direkte MES-Anbindung für moderne Maschinen nutzen
Falls einige Maschinen bereits über digitale Schnittstellen verfügen, können sie oft direkt mit dem ERP-System verbunden werden. Hierfür werden in der Regel standardisierte Protokolle wie OPC UA oder MQTT genutzt.
Vorteile:
✅ Schnellere Integration ohne zusätzliche Hardware
✅ Direkte Maschinenüberwachung über das ERP-System möglich
✅ Automatisierte Datenerfassung ohne Umwege
Je nach Maschinenpark kann eine Kombination dieser drei Methoden die beste Lösung sein..
3. Datenmigration und -validierung
Sobald eine geeignete Integrationslösung gefunden wurde, müssen die Maschinendaten in das ERP-System überführt werden. Dabei ist es wichtig, die Qualität und Transparenz der Daten sicherzustellen.
Dazu gehören:
✔ Validierung der Datenquellen: Sind die erfassten Daten korrekt und vollständig?
✔ Abgleich mit vorhandenen ERP-Daten: Gibt es Inkonsistenzen oder Dopplungen?
✔ Erstellung einheitlicher Kennzahlen: Werden OEE, Stillstandszeiten oder Energieverbrauch in einem standardisierten Format erfasst?
Ein gut strukturiertes Dashboard hilft dabei, die gesammelten Daten übersichtlich darzustellen und mögliche Fehler frühzeitig zu erkennen.
4. Schulung und Support
Die beste Maschinenüberwachung nützt wenig, wenn Mitarbeiter nicht wissen, wie sie die neuen Systeme bedienen sollen. Daher ist eine gezielte Schulung essenziell.
💡 Wichtige Trainingsinhalte für die Mitarbeiter:
- Nutzung der neuen Echtzeitüberwachung und Dashboards
- Interpretation der gesammelten Maschinendaten
- Optimierung von Wartungsprozessen auf Basis der Maschinendatenerfassung
- Fehlerbehebung und Unterstützung durch das IT-Team
Zudem sollte ein Support-System eingerichtet werden, um technische Probleme schnell zu lösen und den laufenden Betrieb zu gewährleisten.
Langfristige Überlegungen für die Integration
Die Integration älterer Maschinen in das ERP-System ist nicht nur eine technische Herausforderung, sondern auch eine strategische Entscheidung. Hier sind einige langfristige Überlegungen:
-
- Regelmäßige Wartung: Stellen Sie sicher, dass alle Maschinen regelmäßig gewartet werden, um einen kontinuierlichen Betrieb zu gewährleisten.
-
- Skalierbarkeit: Ihre Integrationslösung sollte skalierbar sein, um zukünftige Anforderungen und Upgrades berücksichtigen zu können.
-
- Technologische Entwicklung: Halten Sie sich über neue Technologien auf dem Laufenden, die Ihre Maschinenpark-Integration weiter verbessern könnten.
- Maschinenüberwachungssysteme: Diese Systeme unterstützen die Echtzeitüberwachung der Maschinen und verbessern die Produktionsüberwachung erheblich.
Ein langfristiger Plan für die Maschinenintegration und Maschinenüberwachung ist entscheidend für den Erfolg und sollte regelmäßig überprüft und aktualisiert werden, wobei die Maschinenüberwachung als zentraler Aspekt hervorgehoben werden sollte.
Fazit
Die Verbindung älterer Maschinen mit einem ERP-System ist eine strategische Entscheidung, die langfristige Vorteile bietet. Durch eine gut durchdachte Integration, den Einsatz moderner Technologien und eine kontinuierliche Optimierung können Unternehmen ihre Effizienz steigern, Maschinenausfälle reduzieren und ihre Produktionskapazitäten optimal nutzen.
💡 Zusammenfassung der wichtigsten Punkte:
✔ ERP-Integration älterer Maschinen steigert Transparenz und Effizienz
✔ Maschinenüberwachung und Maschinendatenerfassung sind essenziell
✔ KI-gestützte Lösungen wie Novo AI identifizieren Maschinenstörungen automatisch
✔ Skalierbarkeit und Zukunftssicherheit sind entscheidende Faktoren für langfristigen Erfolg
Wer heute auf eine digitale Maschinenüberwachung und ERP-Integration setzt, legt den Grundstein für eine effizientere und wettbewerbsfähigere Produktion von morgen.
➡ Jetzt mehr erfahren: Novo AI für eine intelligente Maschinenintegration 🚀
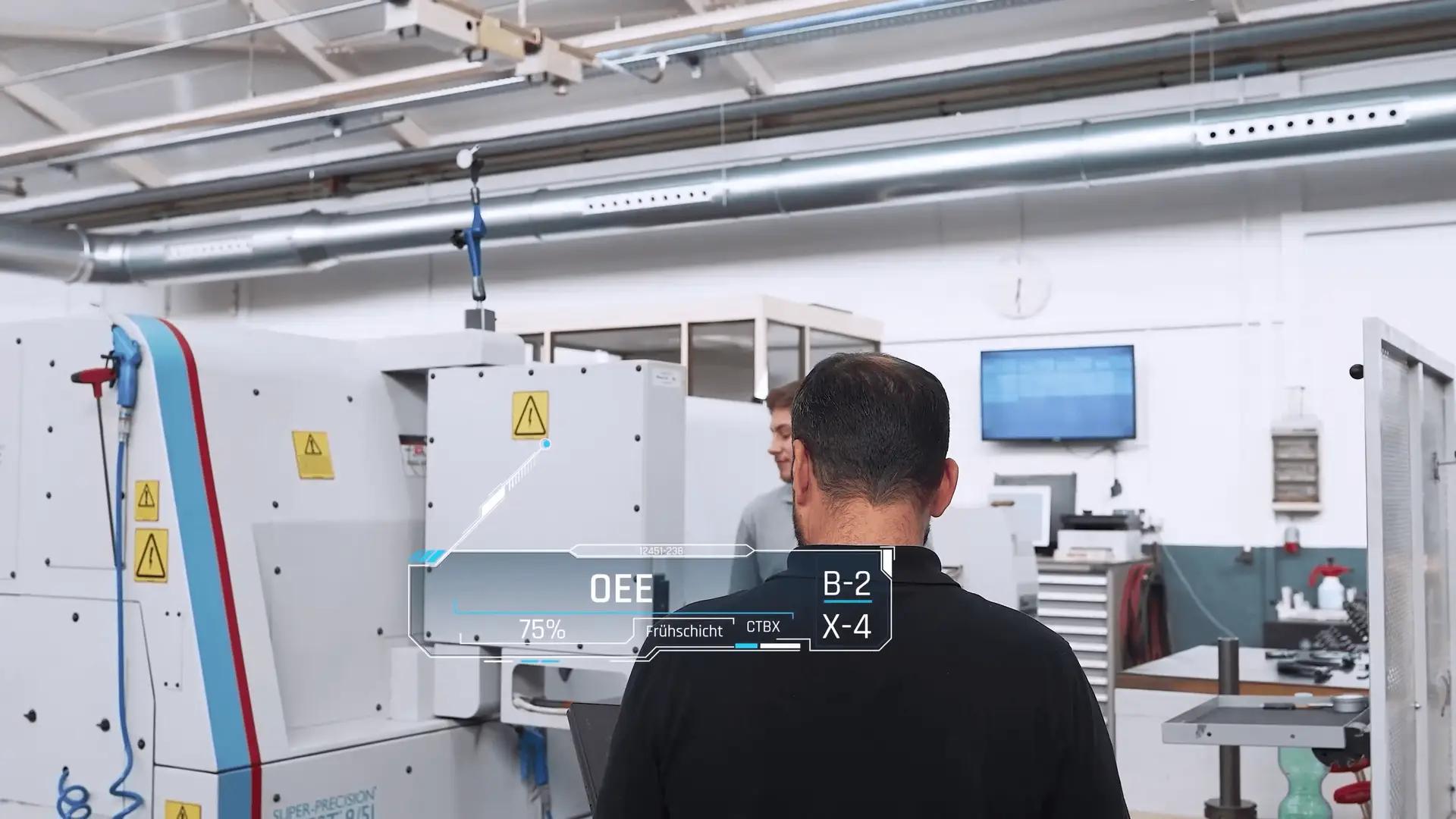
Jetzt starten – ohne Risiko und mit klarer Kostenkontrolle
Digitale Transparenz muss kein Großprojekt sein.
Mit Novo AI starten Sie klein, schnell und risikofrei – schon eine einzelne Maschine reicht aus, um:
-
Bearbeitungszeiten
-
Leerlaufphasen
-
Stillstände
-
Taktabweichungen
-
Energieverbrauch
in Echtzeit sichtbar zu machen.
Egal ob Fräsmaschine, Drehmaschine, Bohrmaschine, Spritzgießanlage, Stanzpresse oder Verpackungssystem – unser KI-Sensor wird in nur 15 Minuten außen angebracht und liefert sofort verwertbare Erkenntnisse – ganz ohne Eingriff in die Steuerung.
Viele unserer Kunden berichten bereits nach wenigen Tagen von echten Aha-Momenten.
Dass Novo AI auf dem renommierten Produktionsleiter-Forum präsentiert wurde, zeigt:
👉 Die Industrie vertraut unserer Lösung – und Sie können sofort starten.
0 Stunden
Produktive Maschinenzeit Gewonnen
0 Stunden
Maschinen Leerlauf Verhindert
0 MWh
Weniger Maschinen Energie Verschwendung
Sie haben eine Frage oder wünschen weitere Informationen? Wir sind für Sie da!